
SEVT.
Solar Electric Vehicle Team
The first solar-powered car team of its kind. Ever.
American Solar Challenge 2021 & 2022 Champs
Bound for ASC 2024.
Scroll
Who We Are.
We are the MIT Solar Electric Vehicle Team - a student group under the MIT Edgerton Center. Every two years we design and manufacture a solar powered vehicle that competes in prestigious national and international competitions.
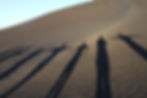
Born by
​
When James Worden came to MIT as a freshman in 1985, he'd already built a solar car. By the time he was 21, he had made 6 of the 10 working solar cars in the country. He then gathered a group of people simply interested in building solar cars. In 1988, Solectrica 5 won the American Solar Cup, from the years 1990-1994 MIT was number one in the American Tour de Sol, and in 1999 Manta GTX was first to cross the finish line in Bridgestone's World Solar Challenge.
With a legacy like that, it's hard to believe that we, as a team, don't quantify our success based on wins and losses. Yet what makes our team so unique is the environment it provides. Our team is student-run, giving our members invaluable experience in project management. We are community-focused, spreading renewable energy initiatives within and beyond the workshop. We focus not on winning, but on creating a well-designed, well-engineered system, and in the process teach all members how to be better engineers. But most importantly, we are a passionate group that believes what makes our team special, are the people on it. That is who we are.
​
Driven by passion. Born by fire. Powered by sun.
Fire.
1985LEGACY.
Powered
By Sun.

WHY DO WE ROCK?
"SOLAR CAR IS JUST AN AMAZING TEAM FILLED WITH AMAZING PEOPLE, IT REALLY ALLOWED ME BE A PART OF SOMETHING SPECIAL, SOMETHING YOU REALLY DON'T GET ANYWHERE ELSE."
ADI / FORMER TEAM CAPTAIN / MIT SEVT
"THIS TEAM HAS TRULY SHAPED MY MIT EXPERIENCE - I HAVE MADE SOME OF MY BEST FRIENDS, CREATED SOME OF MY FONDEST MEMORIES, AND HAVE GROWN SO SO MUCH ON THIS TEAM. MY JOURNEY WITH SEVT HAS BEEN VERY TOUGH YET REMARKABLY REWARDING. IT IS AN INCREDIBLE GROUP OF PEOPLE I'M S0 PROUD TO BE A PART OF."
CAROLINE / FORMER TEAM CAPTAIN / MIT SEVT